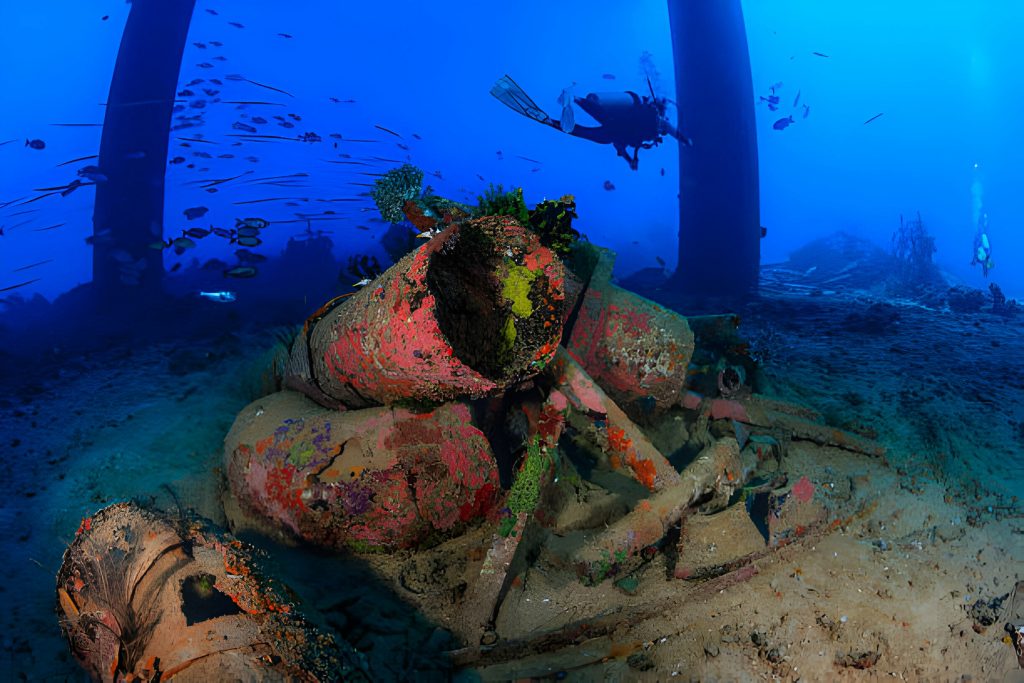
Introduction
As the demand for underwater infrastructure increases—driven by offshore energy, subsea communications, marine research, and climate resilience—so does the need for safer, more efficient, and environmentally responsible construction methods. Traditional underwater construction is labor-intensive, hazardous, and costly. Enter robotic construction underwater—a transformative technological advancement poised to redefine how we build beneath the waves.
The Rise of Underwater Robotics in Construction
Underwater robotics, encompassing remotely operated vehicles (ROVs), autonomous underwater vehicles (AUVs), and robotic arms, has matured significantly in recent decades. Initially developed for inspection and data collection, these systems are now evolving into construction tools capable of performing complex tasks with precision.
Key Technologies Enabling Robotic Underwater Construction:
- ROVs with Manipulator Arms: Enable real-time, human-supervised construction tasks like welding, cutting, drilling, and assembly.
- AUVs with AI-Based Navigation: Perform autonomous surveying, mapping, and transport of construction materials.
- Subsea 3D Printing Robots: Emerging systems that can print concrete and other materials directly underwater.
- Machine Learning Algorithms: Optimize robot path planning, adapt to underwater conditions, and improve task efficiency.
Applications of Robotic Underwater Construction
- Offshore Oil & Gas Platforms
- Installation and maintenance of subsea wellheads and pipelines.
- Real-time inspection and repair with reduced human diver exposure.
- Renewable Energy Infrastructure
- Foundation laying for offshore wind turbines and tidal energy systems.
- Cable trenching and stabilization in deep-sea environments.
- Underwater Tunnels and Bridges
- Robotic placement of prefabricated tunnel sections or reinforcement structures.
- Accurate sediment excavation and concrete placement.
- Undersea Research Facilities
- Construction of modular laboratories or sensor networks for ocean monitoring.
- Disaster Recovery & Environmental Restoration
- Robotic coral reef rebuilding or underwater habitat restoration after damage.
Advantages of Robotic Construction Underwater
- Enhanced Safety: Reduces the need for human divers in dangerous or deep-sea environments.
- Precision and Repeatability: Robotic arms and AI-guided systems execute complex tasks with high accuracy.
- 24/7 Operation: Robots can function continuously in conditions uninhabitable to humans.
- Cost Efficiency: While initial investment is high, reduced labor and downtime lead to long-term savings.
- Environmental Monitoring: Many systems are integrated with sensors to ensure real-time environmental compliance.
Environmental Considerations
Despite their promise, underwater robots must be designed and operated with environmental sustainability in mind.
- Noise Pollution: Some robotic operations generate sonar or mechanical noise that may affect marine life.
- Seabed Disturbance: Improper handling or excessive movement can disrupt sediment and benthic habitats.
- Material Leaching: The use of non-corrosive, non-toxic materials is critical to prevent contamination.
Mitigation Strategies:
- Use of electric rather than hydraulic actuators to reduce pollution risk.
- AI-based navigation to avoid ecologically sensitive areas.
- Integration with real-time environmental sensors to minimize disturbance.
Challenges and Limitations
- Limited Battery Life: Power constraints restrict operation time and range.
- Communication Constraints: Wireless communication is difficult underwater; most systems rely on tethered cables.
- Complexity of Tasks: Robotic systems still struggle with highly variable or unexpected tasks without human oversight.
- High Cost of Development: Cutting-edge robotics remains a capital-intensive field.
The Future Outlook
The future of underwater robotic construction is bright and rapidly evolving:
- Swarm Robotics: Multiple small robots working collaboratively to build or repair structures.
- Underwater Construction Drones: Compact, autonomous systems capable of material delivery and assembly.
- AI-Driven Autonomy: Learning from data to perform tasks without direct human control.
- 3D Printing Underwater: Additive manufacturing of reefs, pipes, or protective structures directly on the seabed.
Conclusion
Robotic construction underwater represents the next frontier in marine engineering and infrastructure development. Combining robotics, AI, and advanced materials, it offers a safer, more sustainable, and efficient alternative to traditional construction methods. As technology advances, underwater robots will not only build the structures we need but also help protect and restore the fragile marine environments they inhabit.